Steel Castings
At Quaker City Castings, we produce high-strength steel castings engineered for durability, performance, and reliability in critical industrial applications.
What Are Steel Castings?
Steel castings are among the most widely used types of metal castings in the world, prized for their exceptional strength, toughness, and versatility. They are produced by melting steel and pouring it into precision-engineered molds that capture every detail of the desired part. As the molten steel cools and solidifies, it transforms into a steel casting that’s built to perform in demanding real-world conditions.
Steel castings are the preferred solution for manufacturing complex shapes and heavy-duty components that would be difficult, time-consuming to produce through machining or fabrication alone. From intricate machinery parts to large industrial housings, these castings deliver consistent strength, durability, and reliability.
At Quaker City Castings, we specialize in producing high-quality steel castings using advanced no-bake sand molding and centrifugal casting processes. Our expertise ensures every casting meets exact specifications and stands up to the toughest applications.
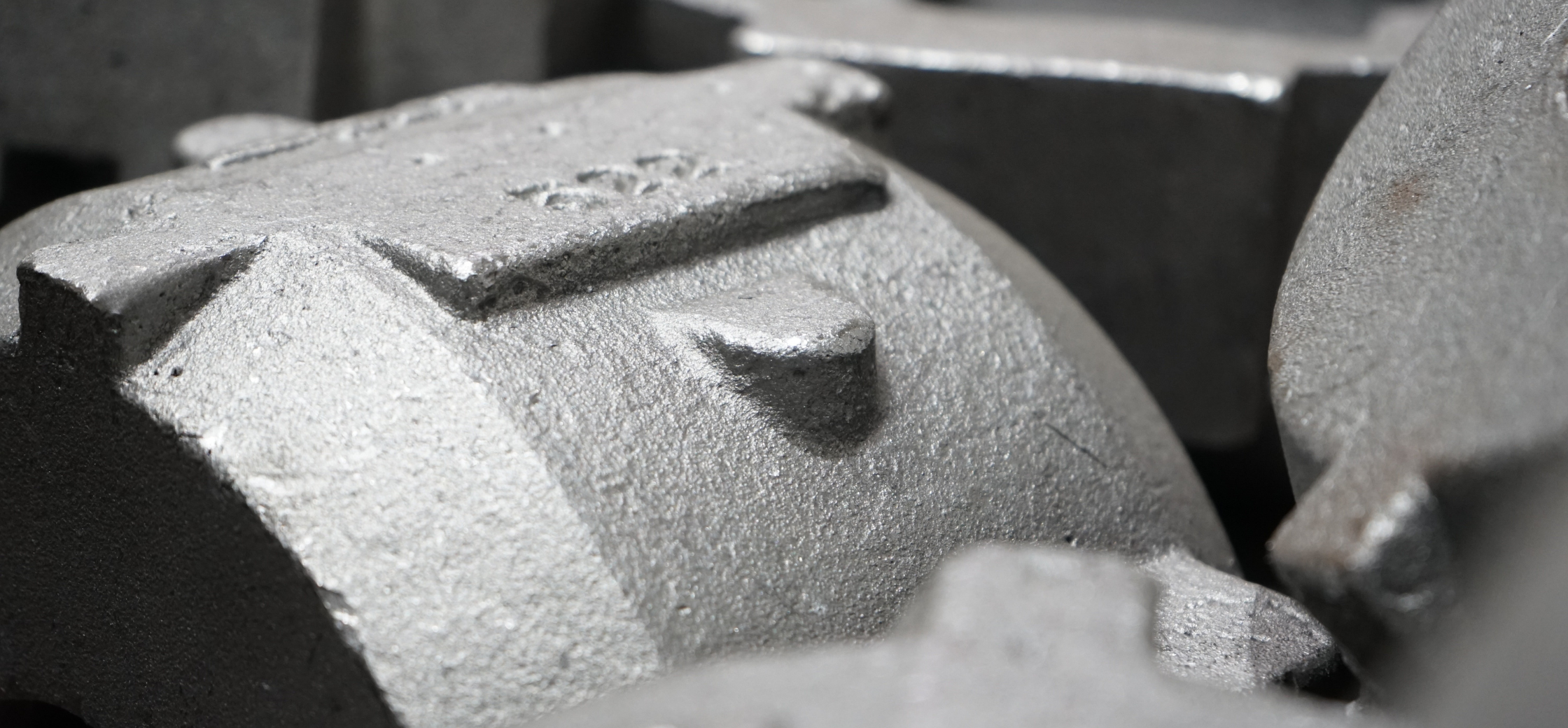
Applications of Steel Castings
Steel castings are essential in various industries due to their versatility and strength.
- Pump & Valve: Built to withstand high pressure, corrosion, and demanding industrial environments.
- Construction: Structural elements, beams, and supports.
- Machinery: Gears, housings, and machine tool parts.
- Railway: Wheels and other critical components.
Steel Casting Methods
At Quaker City Castings, we specialize in two primary steel casting methods: Sand Casting and Centrifugal Casting. These techniques are the backbone of our manufacturing process, enabling us to produce durable, high-quality components with precision and reliability. Our commitment to excellence, combined with our decades of expertise, ensures that every casting meets the highest industry standards.
Steel Sand Castings
At Quaker City Castings, we specialize in no-bake sand casting, a highly efficient and versatile method that allows us to produce precision-engineered steel castings for a wide range of industries. Unlike green sand casting, our no-bake process uses chemically bonded sand to create robust, dimensionally accurate molds that can handle intricate geometries and large-scale components with ease.
Our no-bake sand foundry is designed for maximum flexibility, capable of producing everything from intricate parts that fit to industrial castings, all with exceptional detail and surface quality. This process also supports a wide variety of metals, ensuring that our customers receive exactly what they need, whether it’s high-strength steel, durable iron, or specialty alloys.
We can produce steel castings and iron castings up to 3,500 lbs. All melting is accomplished using a combination of channel induction furnaces and coreless induction furnaces.
Benefits of Sand Casting
This method offers several advantages, making it ideal for a wide range of applications.
- Versatile:From prototype development to high-volume production, our no-bake sand casting process accommodates projects of all sizes.
- Recyclable: The sand used in no-bake casting can be reclaimed and reused multiple times with proper processing, enhancing sustainability.
- Superior Surface Finish and Detail: No-bake molds provide a smoother surface finish and capture finer details than green sand casting.
- Large and Complex Castings: We can produce intricate designs and large-scale components with outstanding strength and durability.
Centrifugal Steel Casting
At Quaker City Castings, our centrifugal casting process is engineered for precision and strength. During centrifugal casting, molten metal is poured into the center of a spinning mold, which rotates rapidly around its axis. The centrifugal force generated by the rotation pushes the liquid metal outward, distributing it evenly along the mold’s interior surfaces.
This process not only ensures superior density and structural integrity but also minimizes impurities and internal defects. The result is high-quality, seamless castings with exceptional durability, ideal for applications such as pipes, cylinder sleeves, and heavy-duty industrial components.
Advantages of Centrifugal Casting
This method is ideal for producing cylindrical parts and offers several benefits.
- High Quality: Produces parts with a fine grain structure.
- Efficiency: Capable of high output rates.
- Precision: Excellent for producing uniform and defect-free castings.
Work With Us
If you’re looking for a reliable partner for your steel casting needs, Quaker City Castings is here to help. Visit our contact us page directly to discuss how we can assist you. We are dedicated to providing solutions that enhance the efficiency and productivity of your operations.